5 Essential Parking Garage Repairs
for Safety and Longevity
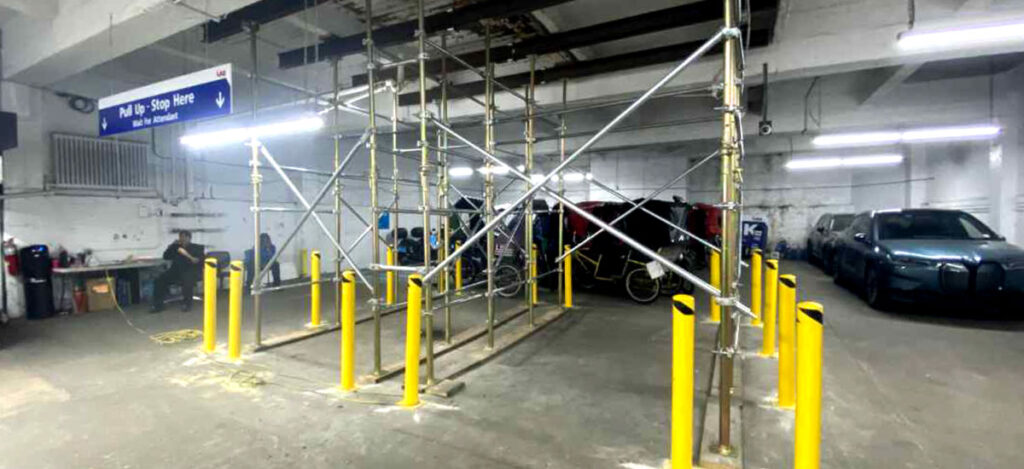
Over time, parking garage structures can develop serious issues if not properly maintained. That’s why regular parking garage repairs are essential; not just to extend the life of the structure but also to ensure the safety of everyone who uses it.
At Avarga Construction Corp., we specialize in parking garage repair in NYC and surrounding area, offering expert services like structural reinforcement, heavy-duty traffic coatings, and comprehensive concrete restoration. Below , we break down five of the most essential repairs every parking garage should consider for long-term safety and durability.
1. Concrete Repairs
Concrete is the backbone of any parking garage. Over time, exposure to vehicle traffic, freeze-thaw cycles, de-icing salts, and moisture leads to visible damage, most commonly cracking, spalling, and delamination. Cracks may seem cosmetic at first, but they allow water to infiltrate, accelerating internal corrosion. Spalling, where surface layers break away, can expose reinforcing steel, while delamination creates hollow, unsafe sections just below the surface. Left unchecked, these issues compromise not only safety but the long-term stability of the structure.
At Avarga Construction, we go beyond surface-level fixes. Our concrete repair approach is built on a combination of precision diagnostics and high-performance materials. Depending on the extent of damage, we employ methods such as:
- Patching localized cracks and potholes with durable, fast-setting repair mortars
- Resurfacing large areas to restore function and visual uniformity
- Using epoxy injections and corrosion-inhibiting agents to strengthen and protect internal components
The key to avoiding costly overhauls? Stay ahead of the damage. Regular inspections allow us to catch early signs of deterioration before they escalate. We recommend annual condition assessments, especially after winter, to monitor known trouble spots and detect new vulnerabilities. Early intervention preserves your investment, minimizes disruption, and extends the service life of your parking structure.
2. Structural Reinforcement
Before any reinforcement begins, we start with a comprehensive structural assessment. This includes visual inspections, non-destructive testing, and load evaluations to identify weakened beams, columns, joints, or decking. Our goal is to understand the full extent of the damage and how it impacts load-bearing capacity, user safety, and long-term use.
Once we identify areas of concern, our team implements targeted structural reinforcement strategies tailored to your facility’s needs. These may include:
- Steel reinforcement to strengthen compromised slabs, columns, and beams
- Replacement of corroded rebar and installation of supplemental supports
- Carbon fiber reinforcement for high-strength, low-profile upgrades
- Application of structural epoxy and bonding agents to restore connectivity
Every reinforcement project we take on complies with local building codes, engineering standards, and New York City requirements. Avarga Construction holds certifications from leading manufacturers, ensuring that every material we use meets rigorous quality standards. Our work will bring your garage to full compliance, protecting property owners from liability and extending the structure’s usable life.
3. Waterproofing Solutions
Water is one of the most damaging elements a parking garage can face. In NYC, where structures are constantly exposed to rain, snow, road salts, and humidity, water infiltration is inevitable without the right protection. Common entry points include cracks in the concrete slab, failed joints, poor drainage systems, and aging or inadequate waterproofing layers. Once inside, moisture accelerates corrosion of the embedded steel, leads to freeze-thaw damage, and compromises the integrity of both concrete and reinforcement.
At Avarga Construction, we specialize in heavy-duty waterproofing systems designed for the unique demands of parking garages. Our solutions include:
- Traffic-bearing coatings that protect driving surfaces from water, oil, de-icing salts, and chemicals
- Elastomeric sealants to fill joints and cracks, creating flexible barriers against water entry
- Waterproof membranes that provide full-surface protection beneath topping slabs or overlay systems
A properly waterproofed parking garage doesn’t just look better—it lasts longer. Our waterproofing systems prevent moisture from penetrating into the structural elements, which dramatically reduces the risk of concrete deterioration, rebar corrosion, and long-term damage. This means fewer repairs, lower maintenance costs, and greater peace of mind. It also ensures your garage remains open and operational without the disruption of emergency closures or costly overhauls.
4. Expansion Joint and Sealant Maintenance
In any parking structure, joints and expansion joints play a critical role in managing the natural movement of the building. As temperatures fluctuate and loads shift, these joints allow the structure to expand and contract without cracking or causing stress to the concrete. Joint sealants also act as the first line of defense against water infiltration—protecting vulnerable connections where slabs meet, or where vertical and horizontal surfaces intersect.
Over time, these protective systems break down. Sealant deterioration from UV exposure, wear-and-tear, and chemical exposure (like road salts or oil drips) is common in high-traffic garages. Once compromised, joints can allow water to seep below the surface, accelerating corrosion and weakening the structure. Joint failure can also create uneven surfaces, leading to trip hazards and increased liability for property owners.
At Avarga Construction, we recommend proactive joint maintenance to prevent bigger problems down the road. Our strategies include:
- Routine visual inspections to catch early signs of cracking, separation, or loss of flexibility
- Timely removal and replacement of worn or failed joint sealants using high-performance, traffic-rated materials
- Inspection and replacement of expansion joint covers, especially in high-movement areas like ramps and transitions
By staying ahead of joint degradation, we help clients avoid costly structural repairs while keeping their garages safe, functional, and watertight.
5. Protective Coatings
Parking garage surfaces take a beating from constant vehicle traffic to exposure to oil, salt, fuel, and changing weather conditions. Without proper protection, these elements can rapidly degrade concrete and compromise structural integrity. That’s where heavy-duty traffic coatings and industrial-grade sealants come in. These coatings form a resilient barrier that shields the concrete from abrasion, chemical intrusion, and moisture, preserving both aesthetics and function.
Even the most durable coatings require regular oversight to stay effective. We recommend annual inspections to assess for wear, delamination, or damage, particularly in high-traffic or exposed areas. Spot repairs and recoating, when needed, can extend the life of the system and prevent costly repairs from neglected wear. Our team can help, regardless of how much recoating needs to be completed.
Trust Avarga Construction Corp. for Expert Parking Garage Repair in NYC
A well-maintained parking garage is not just a functional necessity, it’s a critical component of public safety and infrastructure longevity. At Avarga Construction Corp., we combine decades of experience with advanced technology to deliver repairs that last.
Contact us today to schedule a consultation and learn how we can restore your parking garage to peak condition—safely, efficiently, and reliably.